Researchers deploy EAF steel process for cementitious material production
Sources: Materials Processing Institute, Middlesbrough, U.K.; CMCM staff
A two-year project under the United Kingdom’s Materials Processing Institute will test the efficacy of converting finely graded, demolition concrete-extracted cement paste to new cementitious material using scrap steel melted by an electric arc furnace. Dubbed Cement 2 Zero and proceeding with a $7 million-plus UK Research and Innovation grant, it is poised to prove at commercial scale the Cambridge Electric Cement (CEC) process developed at the country’s flagship university.
Cambridge researcher Dr. Cyrille Dunant pinpointed the chemistry at the heart of CEC, noting strong similarities between ground cement paste and lime-flux used in conventional steel recycling. As scrap melts, the flux forms a floating slag, protecting the liquid steel from ambient oxygen. Once the steel material is transferred, the liquid slag is rapidly cooled, ready for grinding to a powder with chemical and binding characteristics mirroring portland cement.
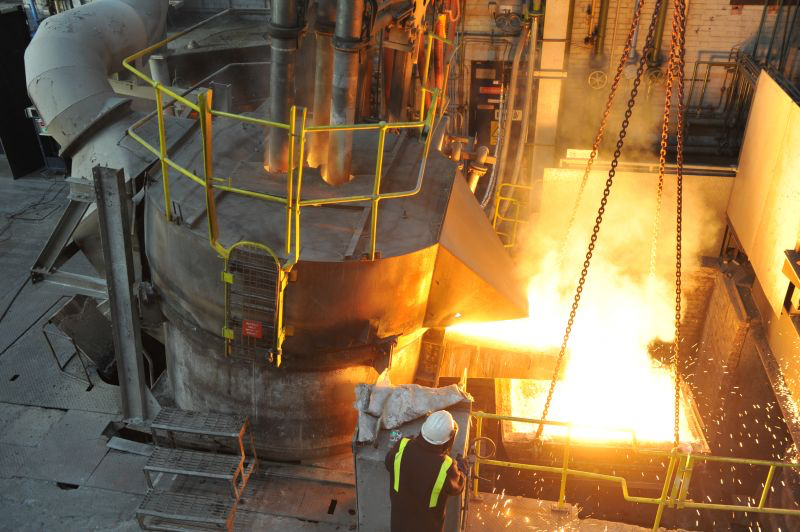
CEC inventors demonstrated their concept in the Material Processing Institute’s arc furnace, propelling the Cement 2 Zero project to a government grant.
“By combining steel and cement recycling in a single process powered by renewable electricity, we could supplement the global supply of the basic construction materials to support the infrastructure of a zero emissions world and to enable economic development where it is most needed,” observes Cambridge Professor Julian Allwood.
“If Cambridge Electric Cement lives up to the promise it has shown in early laboratory trials, it could be a pivotal point in the journey to a zero-emissions society when combined with other innovative technologies,” adds Dr. Phillipa Horton, who joined Professor Allwood and fellow researcher Dr. Dunant behind the CEC invention and patent pursuit. “The Cement 2 Zero project is an invaluable opportunity to collaborate across the entire construction supply chain, to expand CEC from the laboratory to its first commercial application.”
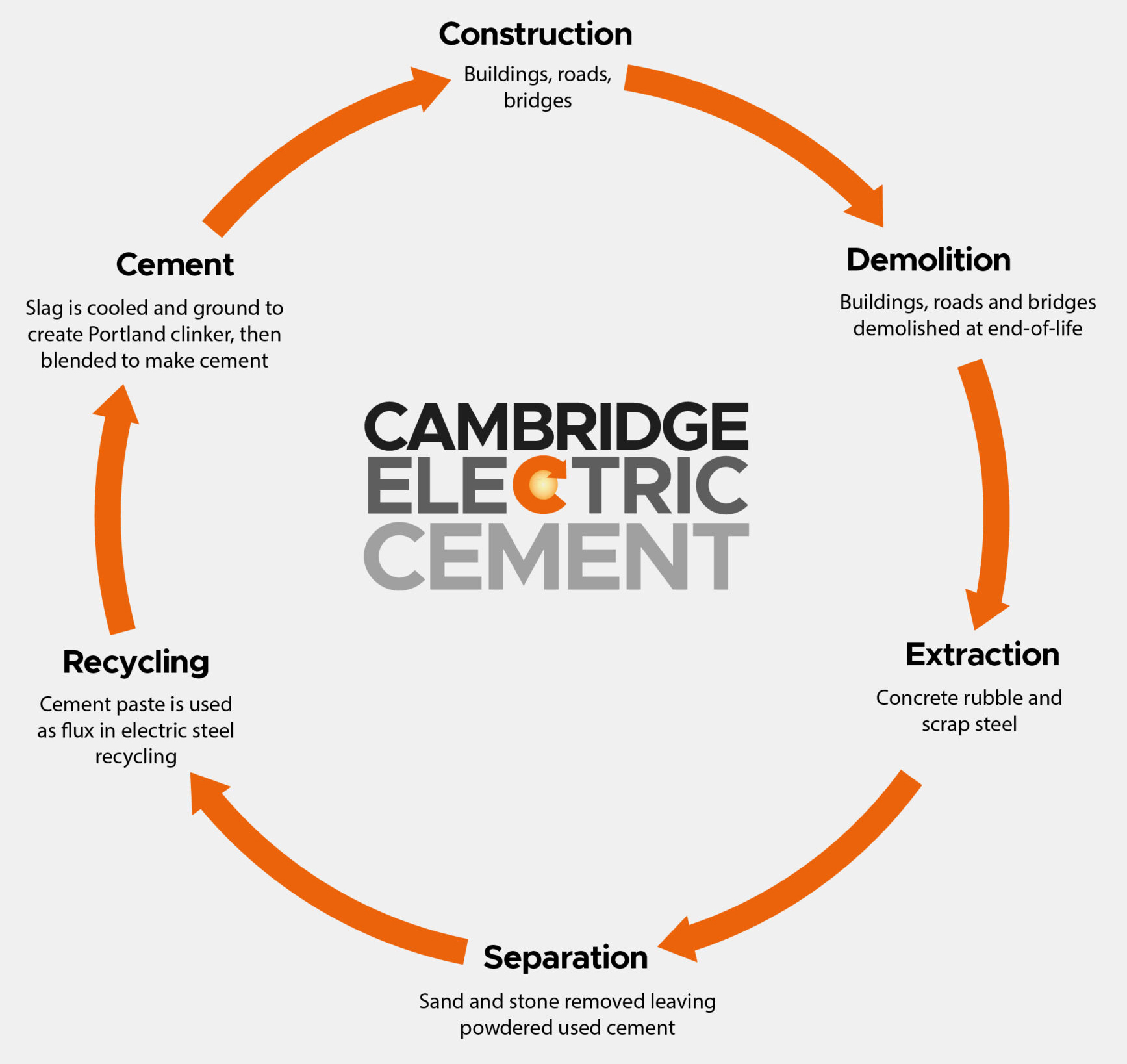
The Cambridge team cites a “virtuous recycling loop” around which CEC eliminates significant emissions of cement and steel production and conserves materials.
“Cement 2 Zero has the potential to make a significant contribution to achieving a zero-carbon society, secure and increase jobs in the cement and steel sectors and challenge conventional production processes, creating high-value materials from demolition waste,” concludes Materials Processing Institute CEO Chris McDonald.
Assisting the Cement 2 Zero project with engineering, test equipment and field demonstrations are the U.K. offices of Atkins and Balfour Beatty; Celsa Steel, the country’s largest concrete reinforcing steel producer; plus aggregate and concrete producers Day Group Ltd. and Tarmac.
Related article
Major cement player logs another year of record CO2 emissions cuts