Cement, steel industry collaboration scales up zero-emissions trials
Sources: Materials Processing Institute, United Kingdom; CMCM staff
Cambridge University researchers have conducted the first scrap-metal trial melt in the Materials Processing Institute (MPI) Cement 2 Zero project, aiming to prove the potential of portland cement clinker production using graded, recycled concrete material as flux in electric arc furnace (EAF) steel milling. The project entails a collaboration of MPI and Cambridge; construction materials producers CELSA Steel UK, Day Aggregates and Tarmac; plus, contractors Atkins and Balfour Beatty. Each party will take a role in research, development, scaling and testing. Tarmac, the U.K. sister operation of the Ash Grove Cement, Oldcastle and CRH Americas Materials businesses in North America, will test trial clinker to understand its grinding properties and assess key performance criteria.
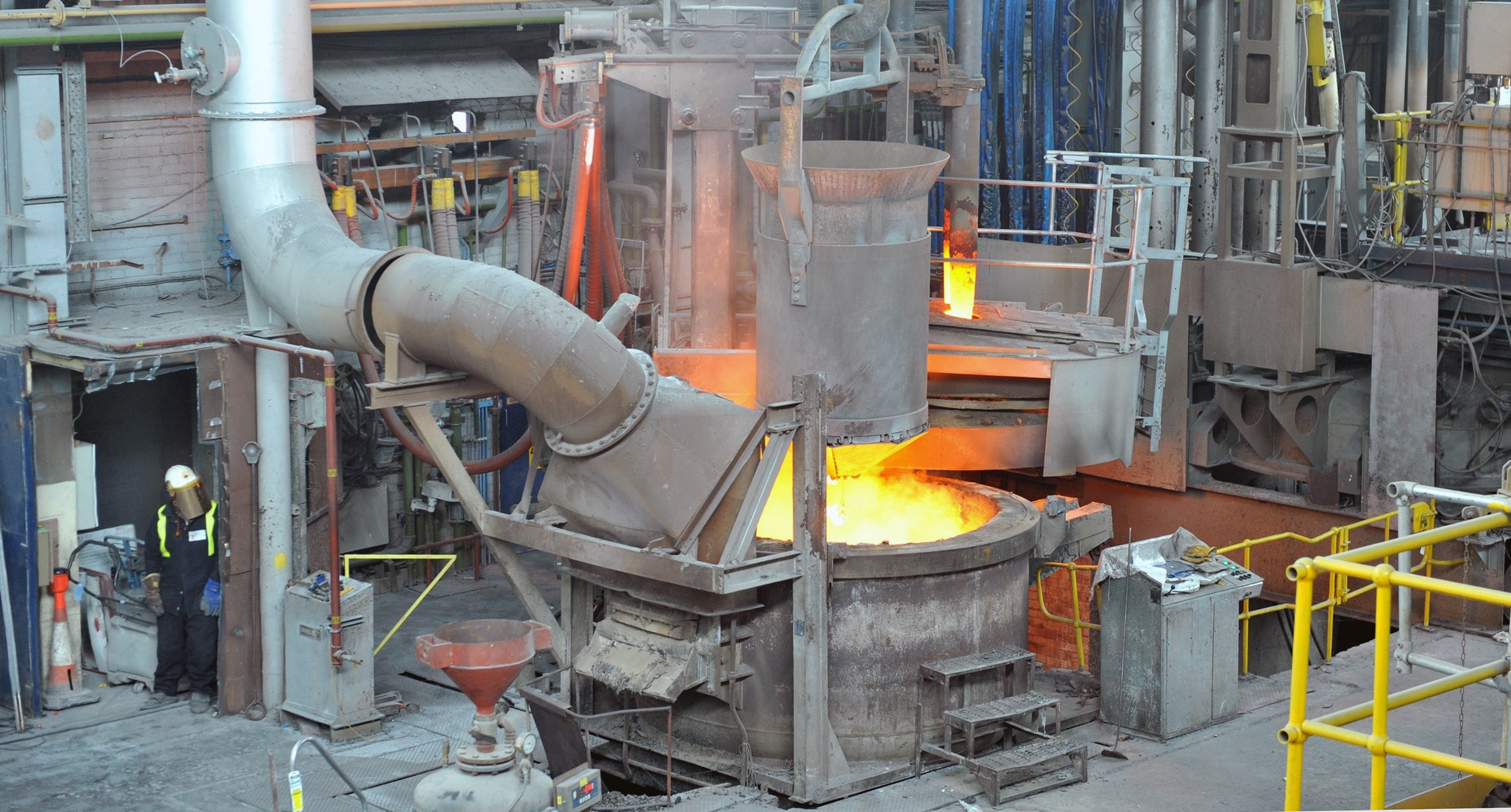
Staged in a 7-tonne electric arc furnace at the MPI Teesside campus in northern England, the trial melt enabled observation of the Cement 2 Zero process at laboratory-plus scale. The R&D team plans three additional scrap melts, followed by industrial-scale trials on the CELSA Cardiff EAF.
Cement 2 Zero process inventor, Cambridge’s Dr. Cyrille Dunant, discovered that the chemical composition of hydrated cement in hardened concrete is virtually identical to that of the lime-flux used in conventional EAFs. The flux floats on molten material and serves the all-important function of oxygen containment. The pilot-scale melts use flux material bearing recycled cement processed by Day Aggregates and international mining and minerals group LKAB, plus CELSA scrap steel inputs. Balfour Beatty and Atkins are defining protocols and detailing projects to test the pilot-scale EAF trial’s material output.
“The initial melt is a critical part of the project and a huge step towards creating a more efficient, environmentally friendly, and resource conscious manufacturing process contributing to the decarbonization of the construction, cement and steel sectors,” says MPI CEO Chris McDonald. “The preliminary findings are encouraging in terms of providing the project team with a much greater understanding of the process and how it can be improved and scaled.”
“This phase has started to provide us relevant insight as to whether the lime replacement material will function for steel making at an industrial scale,” adds CELSA UK CEO Carles Rovira. “We are committed to a Net Zero Pathway and embracing the principles of a circular economy. Investing resources in this ground-breaking collaborative project is a great opportunity for all involved.”
Related article
Researchers deploy EAF steel process for cementitious material production